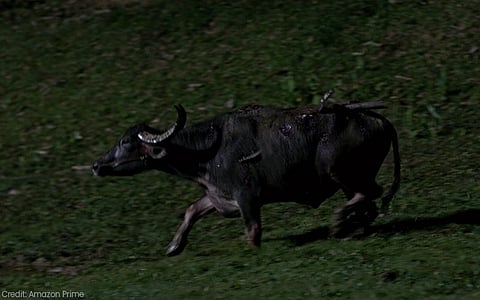
In Lijo Jose Pellissery's Jallikattu, the lines between man and beast begin to blur after an escaped bull goes on a rampage, sparking a village-wide hunt for it. The stampeding animal is fierce, untameable and irate. It's also completely man-made. If you've been taken in by just how realistic it looks, you're not the only one. "Despite showing the Censors all our 'making-of' videos and elaborating on our pre-production process, it was very difficult for us to convince them. They thought we had used a real bull and that caused a slight confusion as we were getting the film ready," says art director Gokul Das.
The film is not only his first collaboration with Pellissery, but also the first time he's had to come up with an entire animatronic animal. His most complex assignment until then had been crafting a realistic elephant trunk, he says. Jallikattu's bull survives fire, weaponized attacks and even a fall down a deep well. Getting it right involved hours of studying Jaws (1975) and Jurassic Park (1993) to figure out how animatronics work, 40 days of intensive work and medical checkups for the man operating it. He talks about how it all came together:
"We know how uncontrollable bulls are right? It is impossible to train or to manage one. Getting permissions too would have been very difficult. We knew it would be very difficult to shoot with the real thing – it won't run when we ask it to, it won't stand when we want. It really is a wild animal. Obviously, there would've been no scope for retakes. So we knew that we would have to make a bull beforehand.
Lijo had a specific vision and the rule right from the beginning was that we would make a bull and only use VFX to fix mistakes, if any. But it turned out such that only 10 percent or even less is animatronics. Even during the shoot, when we were watching it on the screen, we knew we would need to use a lot of VFX.
We made four models using different mechanisms because one model alone would have been difficult to shoot with. So we would always have a spare ready. We had one which could be operated from a distance. Another one, which could work with a person inside it. We made a model with just the bull's head for that POV shot, one with its legs alone and a fifth bull just to be safe. All the models were life-sized. We made a lot of mistakes in the beginning but we kept at it until it started looking real.
Invariably, the bull would need repairs after each day's shoot. It needed constant work. So we would switch it with another one. It's like the bulls were working in shifts. We needed to ensure that it maintained its original look because the continuity could not get disturbed.
It took around 40 days of work (to create the bulls). I had 25 people doing work on them, including welding, moulding, sculpting. The exterior was made using a combination of fibre and silicon. Silicon is what makes it flexible, especially the skin. We did not use real bull skin or leather but the hair on it was real bull hair.
We sourced all of it from India. In the beginning, we thought of sourcing it from Germany, especially the silicon, but it would have been very expensive. Importing such a large amount would have been difficult too. In the end, the bull cost us around Rs20 lakh to make.
The insides were made of motors and other mechanisms which allowed us to make it move. One of our models had space for a person to operate it from the inside but it was difficult for him to see where the bull was going. So we placed a monitor below its head to get a better idea. There were a lot of accidents even then. The person who operated the bull from inside really took a beating. He had to go for medical checkups.
Another challenge was that we were not shooting on an even field. The terrain was unpredictable and a small mistake on our part would mean the whole bull would fall into a ditch. So it was literally a lot of trial and error.
It was very heavy and that made things difficult. There is a metal skeleton inside it because when people jump on it and attack it, it had to stay strong. The fibre too added to the weight but we needed that to make it more durable. We tried to keep reducing the weight though.
There are many limitations to the mechanical bull. We couldn't make it jump. We had to tie it up with ropes to make it do that. It was also difficult to make it lie down or sit in a particular way. To some extent, it is a little easier (to pass off the bull as real) during the night shots because one doesn't get a clear look at it. But the bull we had made was good enough to look real even in daylight. So we weren't worried even if there was a lot of light falling on it.
When I started out as an art director, I didn't imagine I would have to get into animatronics. It was all about making big sets then. In Jalikkattu too, the well was a set we built. It was a structure that stood 25 feet tall because it would have been difficult to shoot all those interior shots had it been actually dug into the ground. The shot of the people piling on top of each other wasn't CGI. It was real.
For the last shot, we had to make a bigger bull that was three times the size. But that was to convey that pre-historic feel of a bigger beast."
(Translated from Malayalam by Vishal Menon)